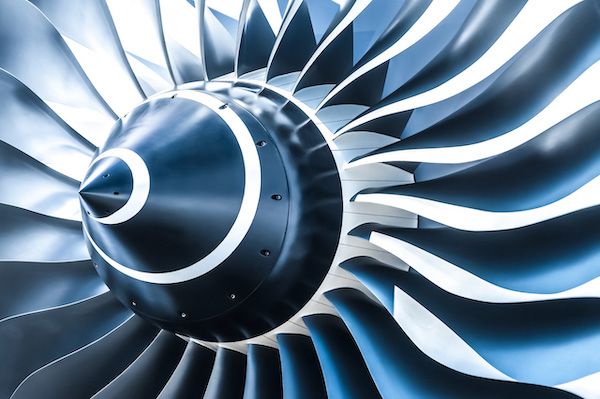
Superalloys, investment casting and speciality steel refractories
Speciality steel refractories that safeguard your reputation
Quality is vital in your highly regulated sector. Your reputation and safety record depend on the purity of the molten material you produce. The refractories that distribute that material round your production line must be of the highest quality, to avoid contamination and reduce your scrap yields.
We know. We have been developing, delivering and supplying advanced refractories to the superalloy and investment casting industries for more than 70 years.
Our expertise is at the primary and secondary melting stage, when the superalloy is melted and cast. By eliminating impurities at the start, we make sure that the parts you produce at the end will meet the highest standards.
To give you more choice, we draw on the expertise of our specialist manufacturing partners. All of them have their own material and processing technologies including casting, isostatic pressing, extrusion and injection moulding. That means we can develop and procure an even wider range of advanced refractories that:
- withstand extreme temperatures and temperature changes
- resist corrosion and contamination for longer
- improve the quality of your end product.
Let’s talk through the options that will give you results of the highest quality.
Our products include customised parts such as:
- crucibles including refractory porous crucibles and dense crucibles;
- metal transfer including a range of lightweight highly insulating ladles and dip ladles, specialist launder systems and transfer tubes
- filtration, including reticulated foam filters in a variety of materials and pore sizes.
Abrasives for superalloys and investment casting. Minimise waste at the primary processing stage
We know the cost per kilogram of your special alloy. We understand you want to minimise scrap yields.
You need high quality abrasives which cut each alloy bar cleanly, leaving the surface smooth and uncontaminated. Without the best abrasive and cutting products you’ll waste this precious material. Something you can ill afford at such a high value per tonne.
To help you reduce these costs we have joined forces with our strategic manufacturing partner CUMI to bring new R&D to abrasives in your industry. Established in 1954, CUMI has state-of-the-art facilities and a proven track record in producing high quality vitrified and resin bonded abrasives. We specialise in the primary processing stage, when the cooled ingots are cut into bars or billet and the surfaces prepared for the next stage of their journey – turbine blades or bespoke automotive components.
We will work with you to cut your superalloy waste bill, with a bonded abrasive blade which is:
- thinner than comparable blades
- as durable as comparable blades
- produced in the quantities you need, when you need them.
See what a difference we will make.